
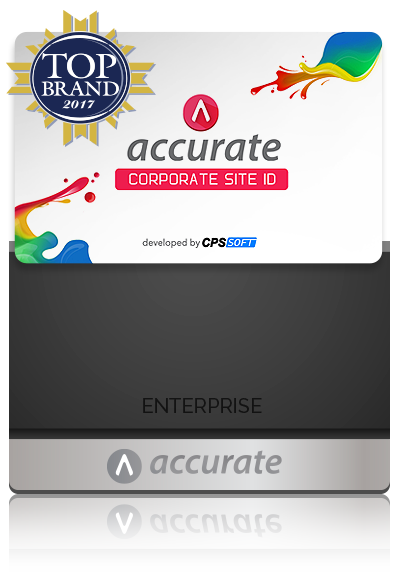
The plastic behavior of composites has two important characteristics different with the metal: anisotropy and hydrostatic pressure sensitivity, which significantly affect the mechanical response of composites. The XFEM can give accurate prediction on the stress concentration and complex crack path without predefining of crack path and mesh.
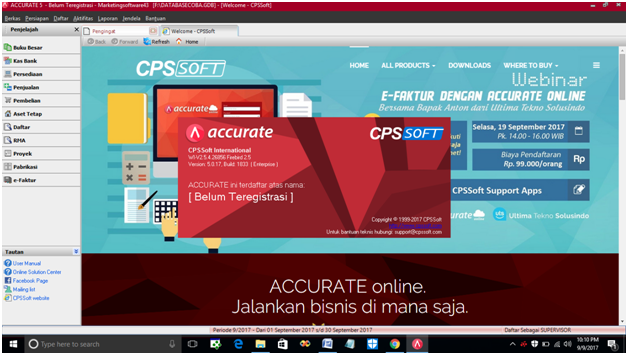
As a solution-dependent crack path method, the extend finite element (XFEM) exhibited a good ability to capture the crack behavior in composites simulation. Nevertheless, they both need to prescribe crack paths before simulation, and will fail when the crack path is complex or unpredictable. In these models, Virtual Crack Closure Technique (VCCT) and Cohesive Zone Model (CZM) were widely adopted to characterize matrix crack for their simplicity. Different with the CMD model, the constitutive models based on fracture mechanics theory have significant natural advantages on simulating crack behavior. These methods can be used to simulate crack but are not widely applied due to their complexity. Hence, some special technologies need to be adopted to simulate matrix crack, such as controlling the mesh size and element shape in the pre-processing or deactivating the crack initiation of the elements on both sides of crack path through subroutine. The traditional CDM cannot capture the stress concentration at crack tip and the propagation path of crack due to its dependency on mesh size and orientation of mesh lines. The post-damage anisotropic behavior is complex, which brings great challenges in the simulation of composites. For instance, in Iosepescu shear test, the failure behaviors of unidirectional laminates specimens with fiber parallel to or perpendicular to loading direction exhibited significant difference.
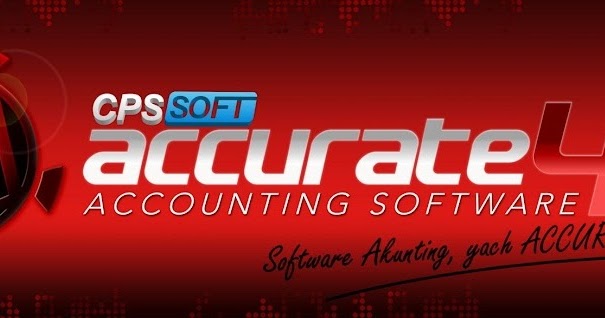
In continue long fiber reinforced composites, the matrix crack mainly extends along the fiber direction, causing anisotropic post-damage behavior. However, there exist many sub-critical damages prior to the final failure in composites, such as matrix crack and plasticity, which have a significant influence on the failure behavior,. The CDM can give an accurate prediction on the failure of composite structures with linear response and brittle fracture. Recently, the finite element method based on continuum damage mechanics (CDM) model is widely adopted to simulate the mechanical response of composites, ,, in which the material is assumed as continuum and the soften process after damage is implemented through stiffness reduction. The application of numerical simulation can reduce the design period and cost greatly. With the wide application of composites in varies industries, the efficient and accurate numerical method as an analysis tool plays more important role in the design and application of composites due to the complex structure and failure behavior of composites.
